Case study
Layout optimization in warehouse pick process
Efficient warehouse operations are crucial for business success, and the picking process plays a crucial role. This case study highlights the impact of using More Optimal software for location assignment (put-away) in a medium-sized warehouse, resulting in a 20% reduction in pick distance and increased productivity.
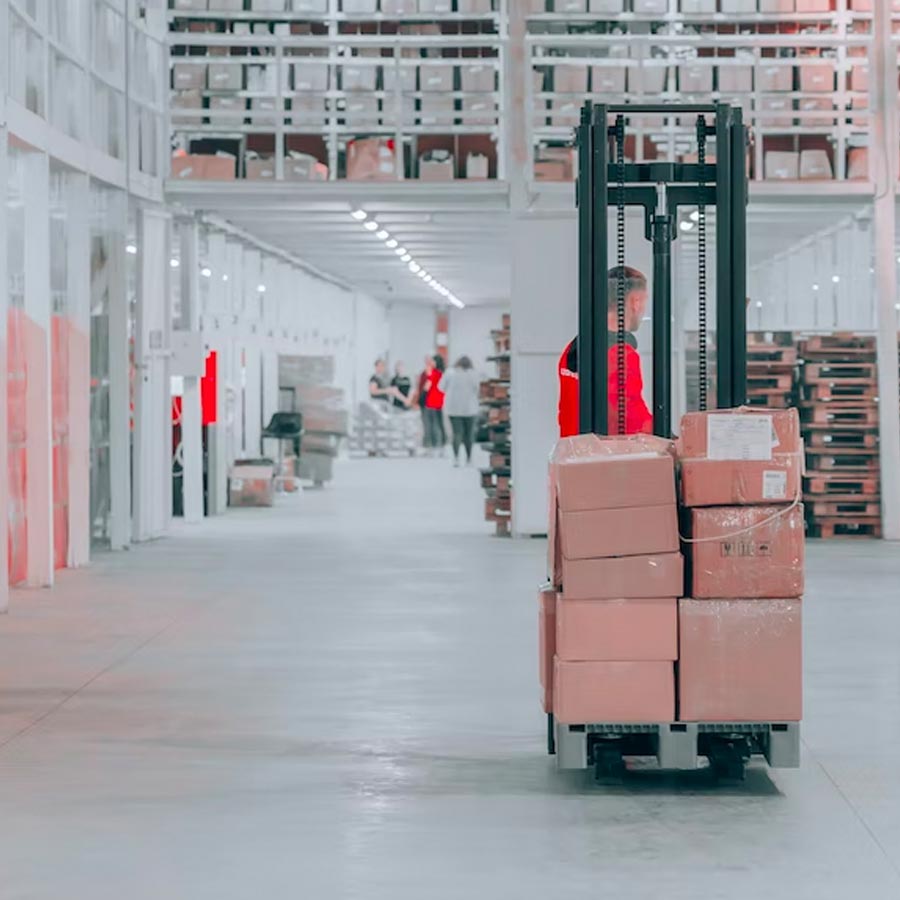
20%
reduction in picking distance
12%
picker productivity increase
35
pickers
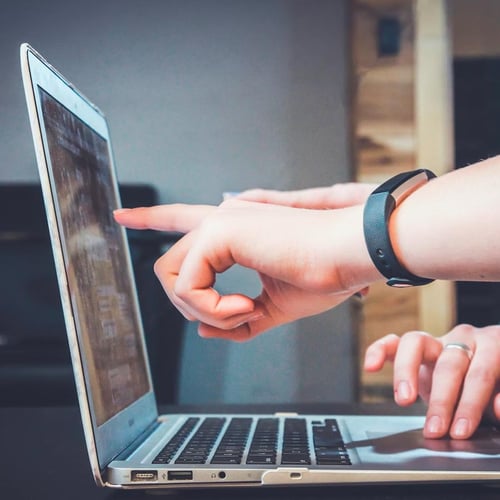
The challenge
After evaluating multiple options, the team chose More Optimal. Based on a sample dataset of one week of picking data, More Optimal quickly displayed heat maps and actual pick routes on the picking area layout. The software's algorithms were used to consider layout scenarios, including the impact of adding shortcuts and one-way traffic in busy aisles.
The More Optimal solution
Before optimization
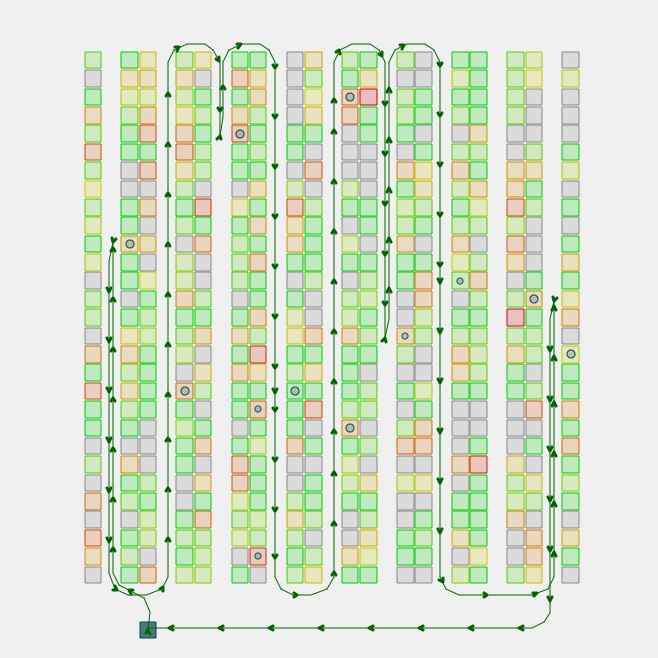
The instant heatmap from More Optimal highlights the diversity of pick location frequency. The heatmap also displays one of the actual picklists and the picker's route, providing valuable insights into the picking process.
After optimization
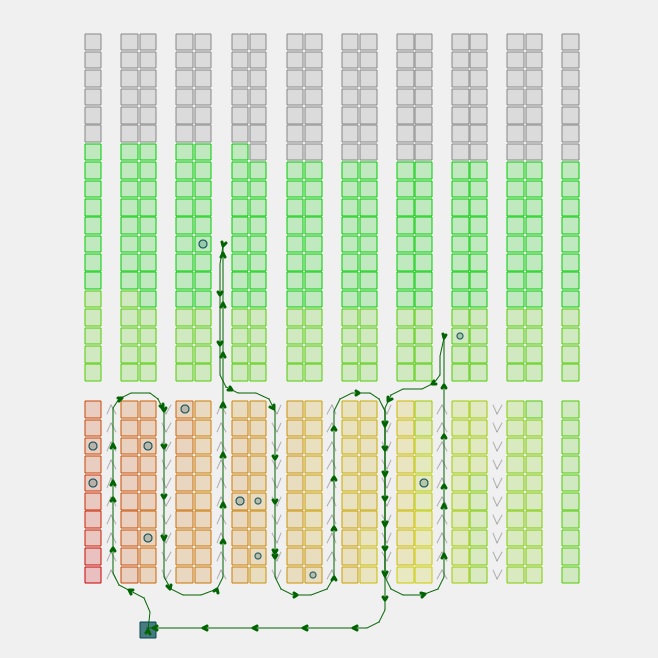
The scenario above was improved by introducing a shortcut, relocating fastmovers close to the depot, and implementing one-way traffic in aisles with fastmovers to eliminate congestion.
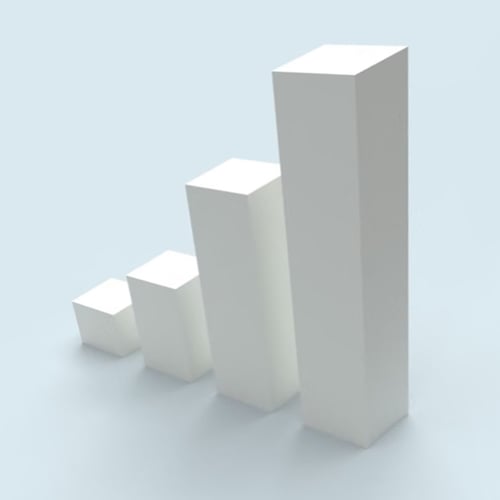
The results
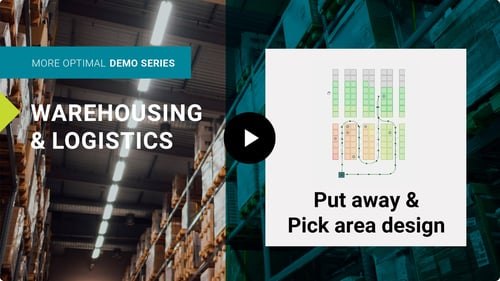