Blog
Customer visit at Schwartzmans BV
How to Outsmart the larger competitors
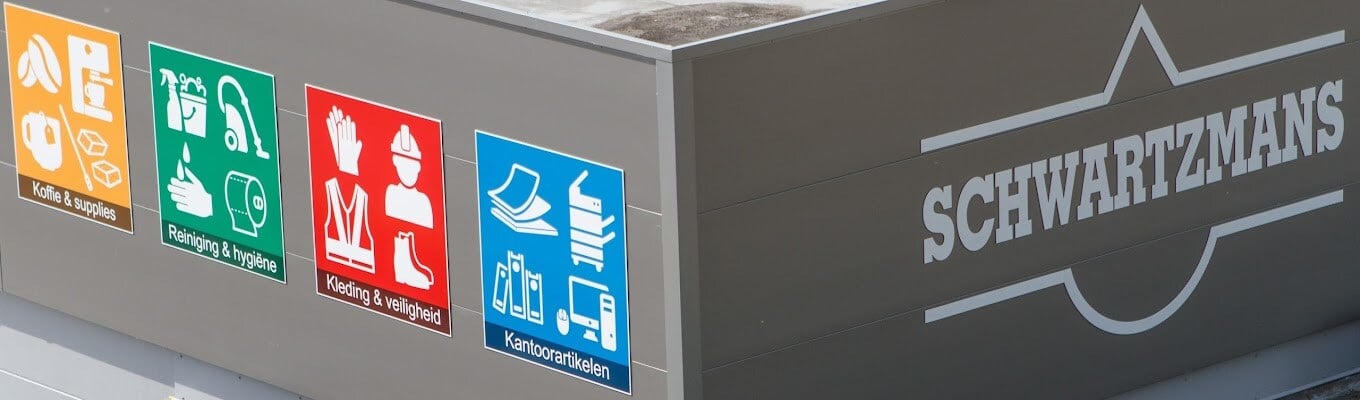
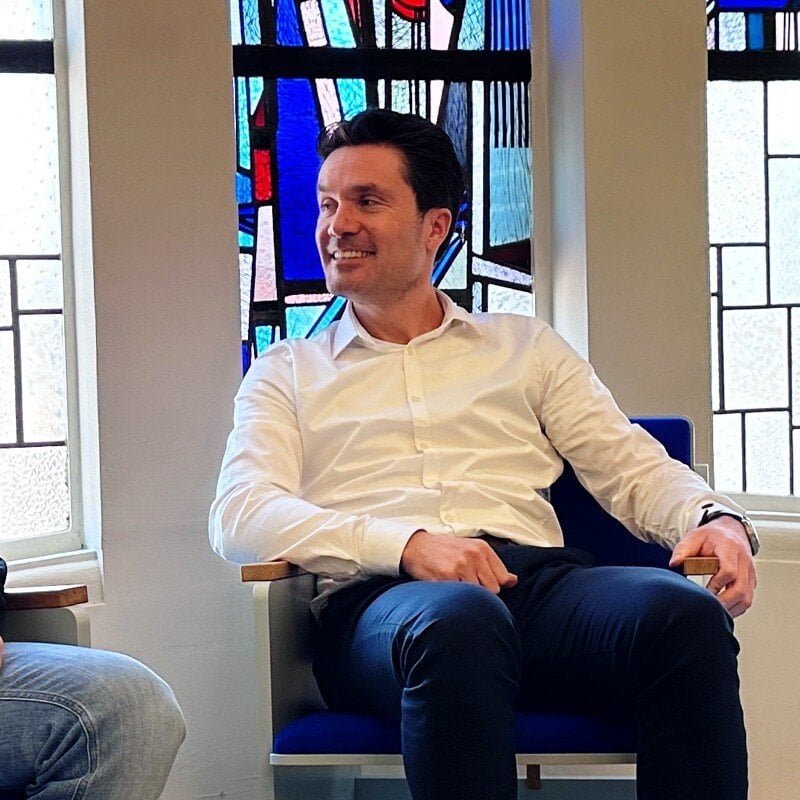
Sander de Vocht
Published on September 18, 2024
I enjoy speaking with the organizations that use More Optimal to make operations more efficient. There are numerous examples ranging from an inland terminal where ships dock daily and hundreds of trucks pick up freight to a ministry unit supported by our (workforce) planning and route optimization.
Some time ago I spoke with William Schwartzmans of the eponymous company Schwartzmans BV in Waalwijk. William and his team sell a variety of facility and utility products with a focus on incontinence, sanitary products and cleaning supplies and accessories.
William has now been working with More Optimal for 5 years and is living proof that supply chain optimization need not be limited to the largest companies. SMEs can also benefit.
The great thing about William is that he doesn't so much want to be the biggest in the market but definitely the smartest! Being the smartest and thus staying one step ahead of big competitors, that's what makes it fun!
Because Schwartzmans takes the entire logistics out of the hands of its customers, it knows the same challenges as large logistics service providers. Inventory management, warehouse optimization, order management and picking and of course delivery through their own logistics equipment and even stock management at the customer's location in their own cabinets.
"The nice thing is that we can innovate so much faster with our relatively small organization" said Wiliam. "I don't have an unwieldy apparatus that I drag along and have to convince about new plans and innovations!"
If we look at the expansions the More Optimal applications have gone through since running at Schwartzmans we see continuous development, nice to see how our flexible approach pays off so clearly here. The application iterates along with the ambitions of team Schwartzmans.
More Optimal plans the daily trips, now also taking into account the electrification of the fleet, which of course has a direct impact on the routes. Routes are rescheduled until the last minute taking into account last minute incoming orders and rush orders. The pick batches that are prepared for transport are of course optimized synchronously with this process.
Scheduling of employees takes place on the basis of the number of pick batches.
Scheduling employees based on stock and orders is something we are working on now. Added to this is an interesting extra dimension, namely decentralized stocking of products in cabinets on site at some customers in the healthcare sector. Here Schwartzmans takes care of all operations within the care facility and thus supports the idea that the care professional can fully focus on what he/she is good at. However, from a planning perspective, this requires a tight forecasting of the cabinet stock as well as the corresponding labor to keep the cabinet up to standard. Here too we used More Optimal to deploy efforts of our employees as smartly as possible based on the data.
Together with Wiliam and his team we continue to innovate, realizing proven applications that we can deploy in other places. A clear win win situation.