Case study
Optimizing the fresh salad production schedule
Producing fresh salads may seem like a straightforward task, but when it comes to mass production in a factory setting, the process becomes highly intricate. Efficient scheduling of production lines can greatly impact a company's overall success.
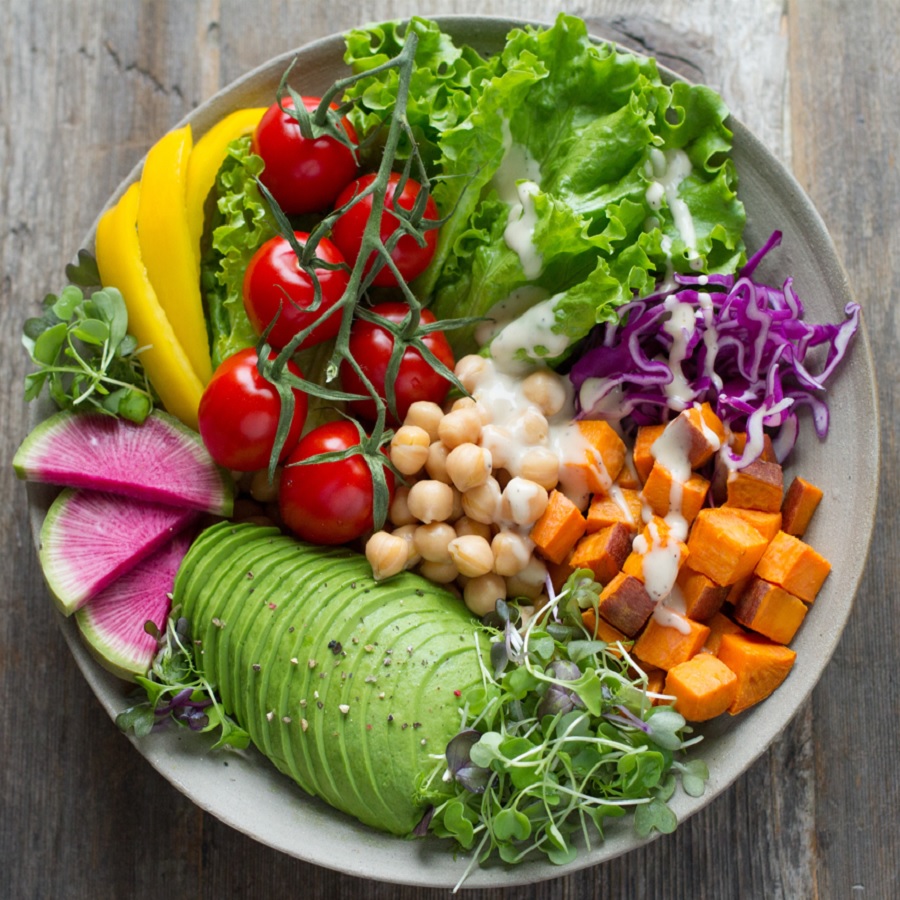
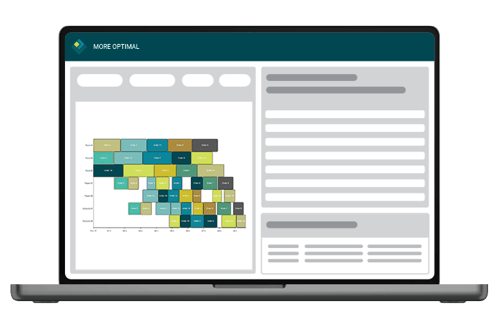
The challenge
After thorough evaluation, the company selected More Optimal as the best solution. The software is built with sophisticated algorithms that improve scheduling by taking into account constraints such as line restrictions, freshness, and order priority. It also seamlessly integrates with the company's existing ERP and shop floor control systems, providing a smooth integration with existing processes.
100+
production lines
4000
orders per day
20+
change-over rules
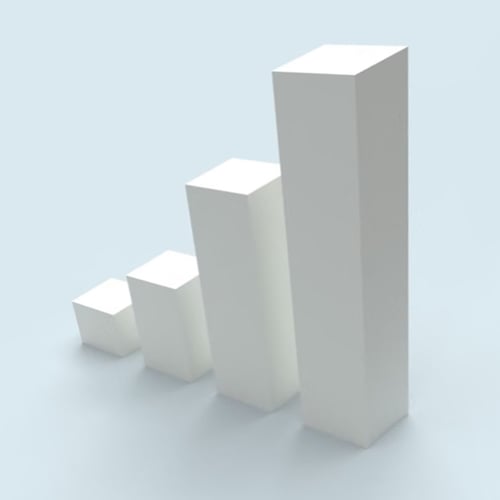
The results
The implementation of More Optimal Software had a significant impact on the scheduling process. Changeover efficiency was improved by 12%, leading to increased productivity and the ability to fulfill more orders per hour. Additionally, the software's optimization algorithms helped to balance workload and resulted in a reduction in labor costs.