Case study
Warehouse workload balancing
The delivery of fast-moving consumer goods (FMCG) from the factory to the end consumer is a complex process that involves a multi-faceted supply chain. FMCG companies rely on third-party logistics companies (3PL) to ensure that their products are delivered on time and in a safe and secure manner. This case study focuses on one such 3PL company that handles a dozen clients for which they are providing logistics services including receiving, storing, and distributing their products.
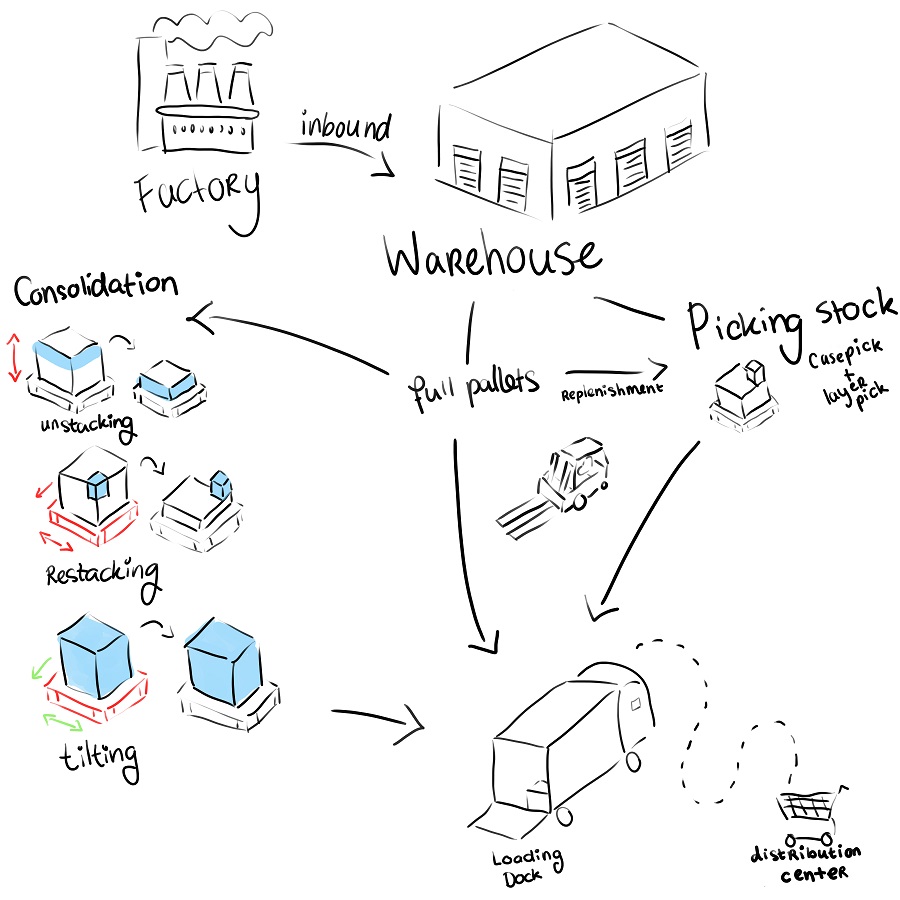
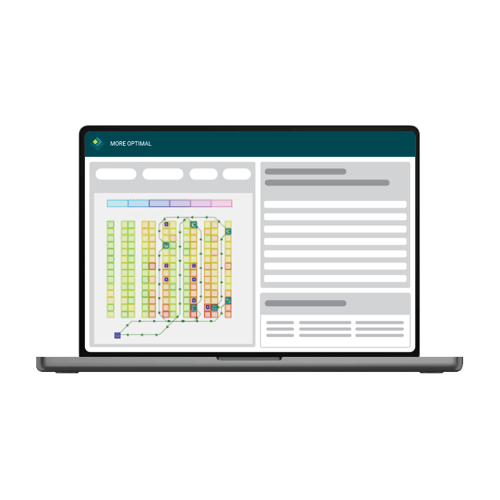
The challenge
For the 3PL company, there are numerous steps involved in getting an order delivered to the right location, including order picking, restacking, and outbound transport. Each of these steps requires significant manpower and resources. Overstaffing leads to an increase in labor and resource costs, while understaffing results in orders not being delivered on time, thereby decreasing customer satisfaction. Therefore, it is crucial to accurately calculate the amount of time required per skill to execute the orders, which helps the company stay ahead of its competitors; especially in times of labor shortages everywhere.
More Optimal Software provides the 3PL company with insights into the workload required to execute all orders, as well as into the ordering behavior of their customers, both past, present, and future. By understanding the order patterns, the company can minimize the number of cases picked and pallets consolidated. The insights into workload are also used for making strategic decisions on how to balance workload structurally, such as switching route days to minimize travel distance and at the same time balancing the workload over the days.
50,000+
pallet places
10%
workload reduction
1000+
orders every day
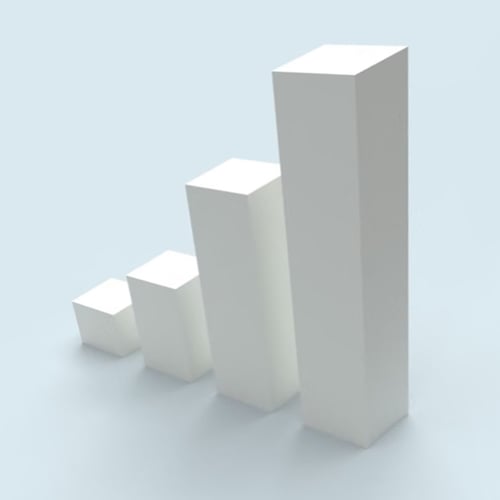
The results
With the implementation of More Optimal Software, the 3PL company can now proactively plan the number of employees needed on any given day to meet the workload requirements. This allows the company to effectively balance its workforce, avoid overstaffing or understaffing, and minimize labor costs while ensuring timely deliveries. As a result, the company has seen an increase in customer satisfaction as well as higher profits. Overall, More Optimal Software has enabled the company to streamline its processes, optimize its workforce, and improve its bottom line.